How To Do Inventory
Learn how to do inventory for your business with our step-by-step guide. Includes free downloads and frequently asked questions.
Updated on January 26th, 2023
The SMB Guide is reader-supported. When you buy through links on our site, we may earn an affiliate commission. Learn more
Inventory is a collection of goods that a business has for sale and/or the materials used to produce goods intended for sale.
Inventory management is the process of ordering, storing, and using your company’s inventory, and is essential when organizing and tracking your company’s goods so that you always have the right products and the correct quantity at appropriate times.
Our Pick
Zoho Inventory
Increase your sales and keep track of every unit with this top rated inventory software.
Affordable.
User-friendly.
How To Do Inventory:
1. Ensure that your forecasting is accurate.
When calculating your anticipated sales figures, your projections must be based on historical sales figures, market trends, competitors' pricing, growth predictions, and the current economic conditions.
2. Engage in the First In, First Out (FIFO) approach for perishable items.
All goods must be filtered out in the same chronological order as they had entered the inventory cycle, especially perishable products with short shelf lives.
3. Engage in the Last In, First Out (LIFO) approach for non-perishable items.
For non-perishable products, you can use the Last In, First Out (LIFO) approach as you don’t need to rotate batches and rearrange your storeroom or warehouse.
TIP: It is recommended to group your goods according to batches with expiration dates as this avoids inventory spoilage, indicates which batches need to be sold first, ensures that your products are not outdated, and allows for easy removal of products if you need to recall a batch.
4. Identify stock with a low-turn pattern.
Stock that hasn’t been selling for more than six months is an indicator that you should stop stocking that item. Consider filtering out the redundant stock through promotions as the freed-up space could be used for in-demand items.
5. Conduct physical inventory counts.
It is a great idea to manually audit your stock by conducting physical counts to ensure that the actual product counts match those in your system. You can also conduct spot-checks on random items if you find regular discrepancies.
6. Real-time stock tracking.
Tracking stock levels constantly helps you to manage the demand for goods. It is recommended to use inventory software which automatically generates tracking reports in real-time so that you can monitor stock levels and identify spikes in demand for specific goods.
7. Ensure quick equipment repair times.
Equipment failure can prove to be costly if it hinders the production of in-demand items. You should regularly monitor your equipment and understand its life cycle to ensure that proper maintenance and necessary repairs are attended to timeously. You can check out our guide on great maintenance management software here.
8. Quality control checks.
It is vital to implement quality control measures to ensure that your goods have maintained their intended standards, are not damaged, are labeled correctly, and have not been rendered outdated or unusable.
9. Employ a stock controller.
A stock controller can help your business by processing orders, receiving materials and goods, and physically checking that orders match. This can avoid costly losses and ensure that stock levels are appropriately managed.
10. Categorize your goods.
Grouping your products in order of priority or higher-value goods can be helpful when deciding how to manage your stock levels, and identifying wasteful expenditure on the redundant or slow-moving stock.
11. Consider drop shipping methods.
Dropshipping is a popular way for businesses to sell products that they don’t physically have in stock. Once an order is placed for a product, the business purchases that product from a third party who is then responsible for shipping that product to the customer. Business is usually conducted online with customers.
Pros and Cons of Drop Shipping:
Pros | Cons |
---|---|
Lessens the cost of opening and maintaining a business. | Reduced profit margins due to the supply chain. |
Your location can be flexible. | Inventory shortages can affect orders. |
Your customers have a wider range of products to choose from. | Complicated shipping costs with different suppliers. |
You don’t have to manage inventory. | Inconsistent customer experience with different suppliers. |
TIP: If you decide to use the dropshipping method, it is wise to use a shorter supply chain in order to maximize your profits. If possible, deal directly with the manufacturer. Multiple parties in the supply chain process will lead to reduced profits due to each party benefiting from their part of the process.
You can check out our guide to supply chain management software.
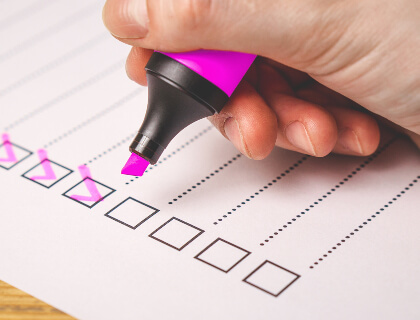
Benefits of Effective Inventory Management:
- You won't invest in an excessive stock that takes up storage space.
- You will be able to sell your stock before it spoils or is rendered obsolete.
- Your customer service processes become more efficient.
- You can prevent losses through returns or theft.
- You can avoid running out of stock with items that are in demand.
- Your funds won’t be tied up in unnecessary stock.
TIP: It is recommended to use inventory management software to ensure the accuracy of your inventory, and avoid running out of in-demand stock.
Inventory Management Classifications.
Inventory management can be classified as either Retail or Wholesale.
Retail inventory management refers to business-to-consumer (B2C) sales and can be further classified as online retail where goods are sold online and offline retail where goods are sold through a brick-and-mortar store.
Wholesale inventory management refers to business-to-business (B2B) sales.
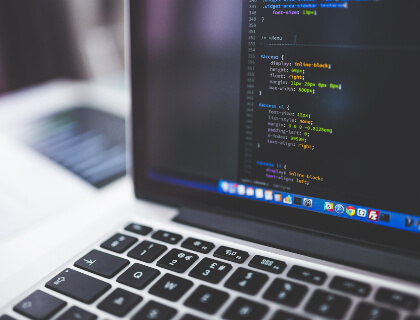
Benefits of great inventory management software:
- Real-time inventory tracking.
- Accurate reporting and forecasting capabilities.
- Improves cash flow and reduces costs.
- Prevents shortages of goods and production materials.
- Easy inventory analysis.
- Improve warehouse/storeroom organization.
- Prevents excessive amounts of goods and production materials.
- Easily accessible through point-of-sale systems.
- Seamless barcode scanning that improves productivity.
- Multi-location inventory management.
You can view our guide on fantastic inventory management software.
TIP: Consider using inventory management software that enables you to automate supply chain processes as this will allow you to generate automated backorder notifications and replenishment reports in real-time, and this will avoid you running out of stock at critical items.
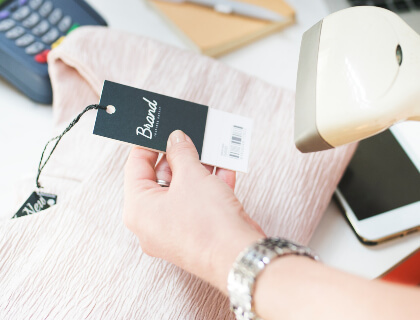
Essential Items for Effective Inventory Management:
- Barcode scanner.
- Mobile computer.
- Inventory software.
- Barcode printer.
- Barcode labels.
How to Get UPC Codes
Learn more about getting UPC codes. Includes information on barcodes, sizing requirements, and a step-by-step guide, as well as FAQs.
Aug 17, 2022
Different Types of Inventory:
Physical inventory can be classified under one of the following four categories:
Raw Materials
These refer to the materials used to produce goods and can be purchased from a third party or manufactured in-house.
Works-in-progress Inventory
These refer to items that are in the production process but are not yet complete for the purpose of selling.
Finished Goods
These refer to items that are already manufactured and are ready to be sold.
Operations, Repair and Maintenance Goods
These refer to items that are used to manufacture goods for sale and may not necessarily form a part of the finished product.
IMPORTANT: A great way to identify and track your products is by using Stock Keeping Units (SKUs). These are product codes that you would label your products with in order to identify and track stock from order forms, lists, and invoices.
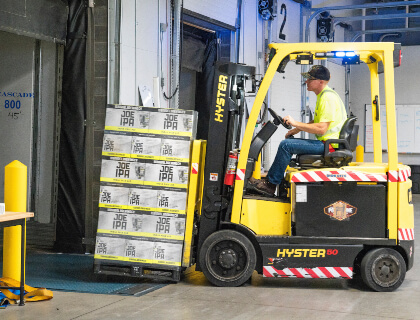
Importance of SKUs for Effective Inventory Management:
- Manages stock availability.
- Identifies product types and locations.
- Monitors sales rates, profit margins, and forecasts.
- Identifies inventory shrinkage due to damage, theft, spoilage, or other losses.
TIP: It is advisable to arrange your SKUs in an alphanumeric system as opposed to using symbols and/or accents as these could lead to formatting issues with your inventory software that may lead to confusion with your actual inventory count.
Common Inventory Management Terms:
Term | Meaning |
---|---|
Barcode Scanner | This is a device that you will use to scan your inventory when sending or receiving goods. |
Bundles | A group of goods sold as a single product with one SKU. |
Cost of Goods Sold (COGS) | This is the cost of manufacturing the goods and includes storage costs. |
Deadstock | This refers to goods that have not been sold for a long period of time. |
Decoupling Inventory | This refers to stock that serves as a safety net in the event that the goods cannot be manufactured due to production failures. |
Economic Order Quantity (EOQ) | This refers to the number of goods that you need to reorder. You must consider the demand and storage costs. |
Holding/Carrying Costs | This refers to the costs that your business incurs to store inventory in your warehouse before it is sold. |
Landed Costs | This refers to the costs associated with transporting and purchasing inventory and may include costs for shipping, import duties, and taxes, and storage. |
Lead Time | This refers to the time that your suppliers take to deliver the goods that you have ordered. |
Order Fulfilment | This refers to the lifecycle of an order from the time of purchase to shipping to delivery. You can check out our guide on order fulfillment software here. |
Order Management | This refers to the processes that govern all aspects of an order, and include fulfillment, tracking, customer support, and payment processing. You can check out our guide on order management software here. |
Purchase Order | This is a document used for business-to-business transactions and outlines product types and quantities, and the agreed prices. |
Pipeline Inventory | This refers to inventory that is in the supply chain process e.g. the manufacturing or shipping stage. |
Reorder Point | This refers to the period when reordering should take place. You must take into consideration the lead times and demand for the product. |
Safety/Buffer Stock | This is inventory that is stored in reserve to safeguard against stock shortages. |
Sales Order | This is a transactional document sent to a customer after a purchase is made but before the order fulfillment cycle is complete. |
Stock Keeping Unit (SKU) | This is a unique code attached to each of your products that will assist you with tracking items and identifying each product. |
Third-Party Logistics (3PL) | This refers to your business using an external service provider to manage warehouse, fulfillment, shipping, and other inventory-related processes. |
Fourth-Party Logistics (4PL) | This refers to your business using an external service provider to manage infrastructure, resources, technology, and supply chain processes. |
Variant | This refers to a unique version of the same product. This could be a different size, color, or shape. |
Performing Manual Inventory Counts:
It is necessary to perform manual inventory counts periodically to ensure that your actual stock count matches the stock count on your system. The process is as follows:
1. Obtain count tags.
You will need count tags that are numbered sequentially in order to track items in the counting process.
2. Inspect all inventory.
All inventory must be inspected prior to the manual count to ensure that they are in a condition to be counted e.g. some items may be dismantled and will need to be assembled in order to be counted correctly.
3. Conduct an inventory pre-count.
In order to make the manual count easier, you can conduct a pre-count to bundle up items that can be packaged. This is particularly useful when you have small items of large quantities that are individually packed. A good example is having nails in packets of 10 that can be bundled into lots of 1000 and stored in a box to make counting easier.
4. Complete all data entries.
Ensure that all warehouse data entry transactions are completed before the counting process begins. This will include all goods dispatched and received, and all transfers.
5. Notify all storage locations.
If you have multiple storage locations, they should be notified in order for them to count the necessary inventory and forward that information to you, as of the court date.
6. Temporarily stop warehouse activities.
It is important to stop all warehouse operations for the duration of the count in order to get accurate figures. This step is critical before the actual counting begins.
7. Create count teams.
Create teams that will count, mark tags, and double-check the counts in order to obtain reliable information from the manual count. These teams will be issued with specific tags and work in dedicated count areas.
8. Verify tags.
Once the count teams have completed their duties, an inventory clerk needs to verify the count tags that have been returned.
9. Compare tag counts to inventory software.
All tag counts must be compared to the counts on your system to ensure that the actual stock on hand matches the figures on your system. It is a good idea to compile a report with all the manually entered data and then compares that to your system-generated reports. Any unusual or conflicting data must be investigated to resolve discrepancies with the counting process.
Manual Inventory Count Sheet - Free PDF Download
Stay on task with your manual inventory process and use our free inventory count sheet.
FAQs:
Is there an app to keep track of inventory?
Yes, many inventory software brands have mobile apps available for your convenience. We recommend Veeqo, SOS Inventory and QuickBooks Commerce.
How do I store inventory in my warehouse?
Your fast-selling items must be easily accessible and close to your delivery area for efficient warehouse operations. Each section of your warehouse should be numbered or labeled to easily identify where specific goods are stored. Perishable items with expiry dates should be stored with the latest consignment at the back of the shelf/section to avoid spoilt goods and wastage.
What kind of inventory management system should I use?
Your inventory management system should have the capability to automate tasks and generate key reports in real-time. It would be beneficial to have a cloud-based system if you work from multiple locations as information would be readily available. We recommend Zoho Inventory, ABC Inventory and Delivrd.
How can I control inventory by manufacturing my own products?
- You will need to track your supply and demand in real-time and ensure that you have sufficient stock levels.
- You will need a consignment of buffer stock readily available in the event of equipment failure, unexpected orders, or delays with obtaining raw materials.
- Conduct regular inventory inspections and spot checks to identify potential issues with your products before they are dispatched or sold.
- Make use of inventory software to create a digital "paper trail" that enables you to track the entire fulfillment process.
How often must I manually count inventory?
Depending on the size of your warehouse, physical inventory counts should be done at least once a month to ensure that the actual stock on hand matches your system. A cycle method is a popular option for many businesses as, at any given time, specific goods are being physically counted. The cycle will end once your entire inventory has been checked over a period of time, and the new cycle will start the process again concurrently.
What are the benefits of automated inventory management processes?
- Your sales can be streamlined across multiple locations.
- You purchasing and order processes can be programmed once.
- You can automatically track stock levels and revenue in real-time.
- You can apply bulk requests for high-order volumes.
What is decoupling inventory/stock?
Decoupling stock is the goods that are kept aside as a safety precaution in the event that your supplier is out of stock or your production process is hindered. It is important to have decoupling inventory available, especially for items that are in high demand, as you may need to access these reserves for customer orders.
How do I make an inventory list?
You can use one of the inventory list templates available in Microsoft Excel, or you can download an inventory list template.